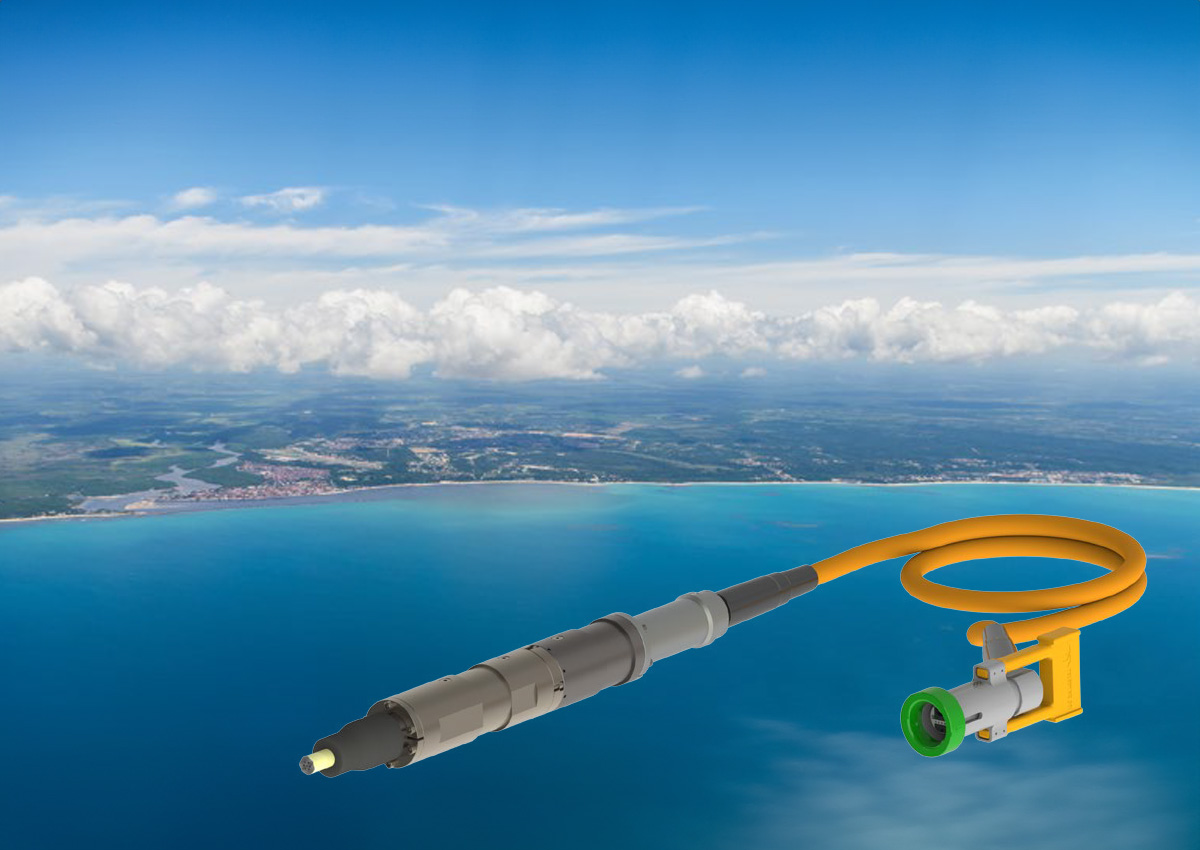
Background
For Phase II of Shell’s BC-10 Block, situated 120 kilometers southeast from the coast of Brazil, the use of water injection for reservoir boosting required a thorough knowledge of the geological structure of the fields. OYO Geospace, a prolific manufacturer of geophones, hydrophones, and reservoir monitoring equipment, was contracted to provide over 100 kilometers of seismic monitoring hardware in a water depth of 1,700 meters.
What were the project challenges?
Although they provided the word’s first Life of Field Seismic (LoFS) system for Shell’s Valhall field in 2003, OYO Geospace faced a unique challenge in the design of this new LoFS system. First, the sheer amount of data collected from the hydrophones required high bandwidth communication back to the shore. Secondly, interfacing to the existing Phase I cable infrastructure imposed considerable dimensional and reliability constraints to the system. In their proposed design, OYO Geospace required a large number of robust cable terminations, supporting both electrical and optical throughput.
What were the innovative technical solutions available for the project team?
The Teledyne Oil & Gas Field Assembled Cable Termination (FACT) was a superior choice for this mission-critical application, due to its low risk field assembly, excellent post-deployment field reliability, and also to the complementary pre-deployment field support supplied by Teledyne for every termination delivered.
The option of separating the optical and electrical cable terminations was available; however, this would have essentially doubled the number of terminations required. With countless optical and electrical FACT assemblies already proven in the field, Teledyne’s goal was to utilize as much historical FACT technology as possible in the development of a consolidated electro-optical (or Hybrid) FACT, while improving the overall robustness and simplifying the field assembly process.
What was the final engineered technical solution?
The Teledyne Oil & Gas team developed a Hybrid FACT assembly that combined the most reliable components of the existing Electrical and Optical FACTs already in the product line, and proven with years of field reliability data.
Though the combined optical and electrical termination assembly introduced new elements, the Hybrid FACT maintained several hallmarks of Teledyne Oil & Gas technology, including the use of standard-sized shells for short lead times, and a standard redundant sealing philosophy.
At the TOG factory, the pressure-balanced, oil-filled (PBOF) section of the termination is subject to a standard Factory Acceptance Test (FAT). This assembly includes the FACT optical penetrator, the pass-through solder pots for the electrical conductors, and any ancillary equipment on the PBOF side (junction boxes, distribution units, or hybrid wet-mate connectors, for example). Then, in the field, the electrical and optical sections of the cable are carefully broken out into individual dual-sealed atmospheric regions. These independently sealed regions are then joined to the pressure balanced oil field region. The result is a surprisingly simple, yet high reliability, low-risk field termination.
What were the benefits of selecting this particular approach/solution compared with the others proposed?
The design of the new Teledyne Oil & Gas Hybrid FACT system consolidates the best features of the Electrical and Optical FACT units into a single comprehensive structure that allows for lower initial costs and lower total life costs. The single qualified structure drives greater operational efficiencies through the reduced number of overall terminations to build, manage and deploy. The FACT termination is assembled and tested in less time than traditional terminations which enhances efficiency and lower the overall program cost.
Operational risk reduction follows, as the proven elements of the FACT design continue the practice of true factory build and acceptance testing of the high risk elements of the termination, while including the proven reliability of the cable side fixtures and isolation design elements of the field assembled portion to eliminate the known failure risks.
Although an all-optical seismic monitoring system was considered, the cost and proven history of the OYO Geospace electrical hydrophone made it a superior choice for the Shell BC-10 expansion. The development of the Hybrid FACT product allowed the reliable, high-bandwidth distribution system needed for continual data transmission to ensure the seismic integrity of the field over its operational lifetime.